Рельсосварочное предприятие
Описание
1. Введение
Современные требования, предъявляемые к железнодорожному транспорту, обуславливают увеличение скорости движения подвижного состава и рост нагрузки на ось, что усиливает динамические удары при прохождении стыков рельсов. В связи с этим, очень актуальной является проблема создания железнодорожного пути без накладочно-болтовых стыков рельсов, что надежно обеспечивает контактная стыковая сварка длинномерных рельсовых плетей в условиях специализированного рельсосварочного предприятия с последующей укладкой их в путь.
Представляем типовой проект рельсосварочного предприятия, обеспечивающего производство рельсовых плетей из рельсов различных типов и марок сталей.
Рельсосварочное предприятие состоит из подъездных путей, склада сырья, производственного корпуса с установленным оборудованием и пристроенных к производственному корпусу вспомогательных помещений.
Основной производственный корпус выполнен из каркасных металлоконструкций на монолитном железобетонном фундаменте. Наружные стены выполнены из стеновых панелей с утеплением, содержащих оконные блоки из металлопластиковых стеклопакетов. Кровельное покрытие выполнено из сборного профилированного листа с тепло - и пароизоляцией. Пол выполнен из монолитного железобетона с различными покрытиями, зависящими от производственного назначения помещения.
Здание оборудовано системами водоснабжения и канализации, отопления и вентиляции, холодоснабжения, электроснабжения, воздухоснабжения, связи, автоматической пожарной сигнализации и громкоговорящей связью.
Вдоль технологической линии производственного корпуса размещены административные, бытовые, производственные и вспомогательные помещения.
В них располагается вентиляционное оборудование, трансформаторная подстанция, компрессорная, склады, вспомогательные цехи, медпункт, офисные помещения, гардеробные, душевые, туалеты, столовая, кладовые запчастей и инструмента, и др.
Проектирование рельсосварочных предприятий и расстановка технологического оборудования зависят от следующих параметров:
- рельсы новые или старогодные;
- длина рельсов;
- максимальная длина свариваемых плетей;
- климатические условия;
- отводимые площади под строительство РСП и т.д.
Общие принципы построения работы рельсосварочного предприятия по сварке рельсовых плетей остаются неизменными, но отдельные особенности формируются в каждом конкретном случае в соответствии с базовыми параметрами и требованиями заказчика.
Применяя комплексный подход к удовлетворению потребностей заказчика, мы осуществляем изготовление и поставку нового рельсосварочного оборудования, производим шефмонтаж и пусконаладочные работы, обучение персонала, осуществляем капитальный ремонт и модернизацию сварочного оборудования, как собственного производства, так и других производителей, гарантийное и послегарантийное обслуживание, поставку запасных частей.
2. Типовая схема технологического процесса
Опыт работ по созданию рельсосварочных предприятий и внедрению технологии контактной стыковой сварки рельсов показал, что для изготовления рельсовых плетей целесообразно применять следующую схему технологического процесса:
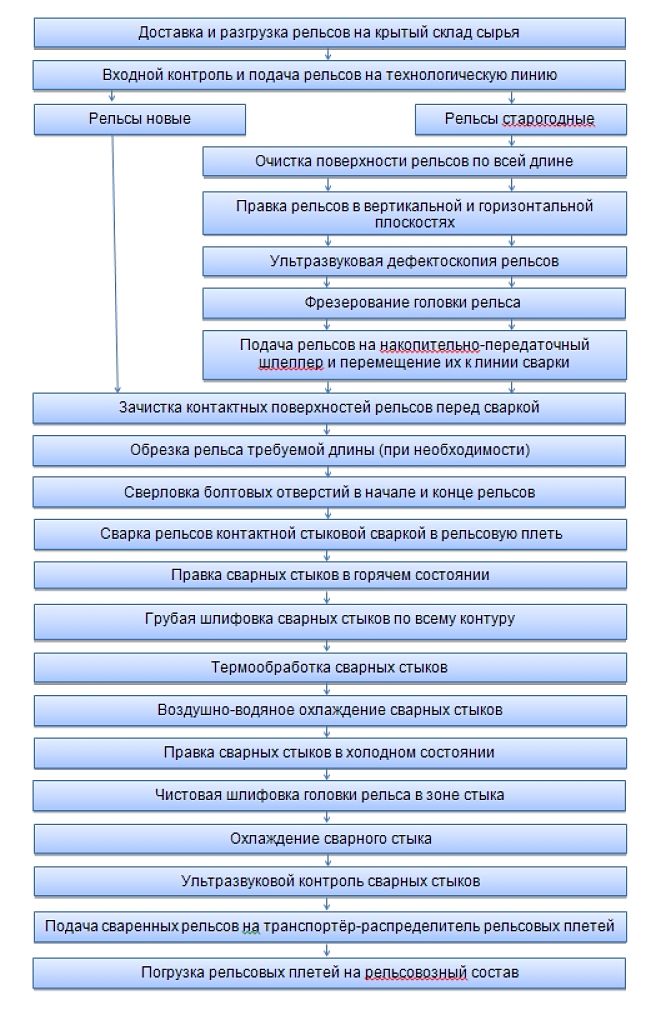
3. Технологический процесс рельсосварочной линии
3.1. Доставка рельсов осуществляется по технологическому железнодорожному подъездному пути или автомобильным транспортом. Выгрузка и складирование рельсов производится на площадку складирования сырья. Площади склада обеспечивают возможности хранения месячной нормы производительности предприятия.
Склад сырья представляет собой крытое помещение из профилированного листа и имеет сквозные проезды. Разгрузка рельсов производится радиоуправляемыми электрическими талями со специальными захватами на горизонтальные площадки в штабели, между которыми проложены секции универсальные рольганговые транспортирующие типа СУРТ-01. Секции предназначены для транспортировки рельсовой плети по технологической линии сварки рельсов.
Секции оборудованы питающей и управляющей электроаппаратурой, которая при монтаже включается в единую линейную схему с выводом на пульт управления по участкам. Каждая рольганговая транспортирующая линия - это единая неразрывная технологическая цепочка от одного поста до другого.
3.2. Перед подачей на поток, производится входной контроль рельсов. Проверяется наличие приемочных клейм и маркировки. Производится визуальный осмотр на наличие поверхностных дефектов.
Погрузка рельсов на технологическую линию производится радиоуправляемыми электрическими талями со специальными захватами (аналогично выгрузке на склад сырья).
Со склада приводными рольганговыми секциями рельсы подаются на операцию зачистки.
3.3. Зачистка контактных поверхностей рельсов под сварку производится на станке типа СЗ-03 одновременно двух смежных рельсов.
Чистота обработанной контактной поверхности соответствует современным требованиям для контактной стыковой сварки рельсов и позволяет получать оптимальные электрические параметры теплового баланса оплавления, что очень важно для получения качественного сварного соединения. Станок укомплектован фильтровентиляционной установкой.
3.4. С помощью рельсорезного станка, при необходимости, производится обрезка рельса в необходимый размер, нарезка контрольных экземпляров рельсов для подготовки испытания сварных стыков. Пильная рама станка располагается на двух колоннах, что многократно увеличивает жесткость и точность резки.
3.5. По концам рельсовых плетей для бесстыкового пути с помощью рельсосверлильного станка просверливаются три болтовых отверстия. Станок осуществляет автоматическую подачу сверла и регулировку сверла по высоте, укомплектован прочными спиральными сверлами, быстрозажимным устройством и зажимными шаблонами под рельсовую пазуху различных типов рельсов. Сверление отверстий производится переносным рельсосверлильным станком, установленным на специальной рольганговой секции. Приводными рольганговыми секциями рельсы подаются на операцию сварки.
3.6. Сварка производится машиной типа МСР-6301А, предназначенной для контактной стыковой сварки с пульсирующим оплавлением рельсов в стационарных условиях. Машина обеспечивает центровку рельсов перед сваркой по оси рельсов и по высоте головки и съем грата по всему периметру стыка непосредственно после сварки.
Система управления работой машины выполнена на базе промышленного компьютера и обеспечивает:
- задание и контроль технологических параметров, определяющих качество сварного соединения;
- контроль состояния исполнительных механизмов машины;
- контроль состояния силовой электрической части машины;
- предоставление оператору в режиме реального времени информации о прохождении технологического процесса сварки;
- накопление и хранение информации о протекания процесса сварки каждого сваренного стыка;
- выдачу паспорта на каждый стык;
- самоконтроль и самодиагностику.
Вредные выбросы, образующиеся при сварке, локализуются и удаляются местной вытяжной вентиляцией.
3.6.1. Современные требования к безопасности движения железнодорожного транспорта не позволяют ограничиваться только паспортом сварного стыка, выдаваемым сварочной машиной. Для проверки сварных стыков производят выборочный контроль соблюдения заданного режима сварки путем испытания контрольных образцов на статический поперечный изгиб на прессе малогабаритном специальном типа ПМС-320.
Система управления пресса выполнена на базе промышленного компьютера. Она позволяет производить запись и хранение процесса испытания сварного соединения, паспортизирует каждый излом, выдает нагрузочную кривую процесса и позволяет в режиме реального времени осуществлять контроль над процессом.
Пресс устанавливается вне технологической линии в районе сварочной машины.
3.7. Сваренный рельсовый стык подается на установку правки горячих стыков типа УПС-02. Установка предназначена для правки горячего сварного стыка в целях соблюдения требуемой геометрии поверхности катания и головки рельса. На установке производится правка рельса на базовой длине 1700 мм в горизонтальной и вертикальной плоскостях.
Проверяется прямолинейность сварного стыка по поверхности катания и с рабочей грани головки рельса.
На раме УПС-02 установлены два опорных ролика, по которым перемещается сваренный рельс, два гидроцилиндра для правки в горизонтальной плоскости, гидроцилиндр для правки в вертикальной плоскости. На стяжках смонтированы ролики и упоры, ограничивающие перемещение рельса при правке. Управление перемещением упоров гидроцилиндров осуществляется джойстиком на четыре направления, питание гидроцилиндра осуществляется от гидростанции.
После правки рельс подается на операцию грубой шлифовки сварного стыка.
3.8. На стационарном посту грубой шлифовки типа ПГШ-01 с помощью шлифовальных машин производят абразивную обработку стыка по всему периметру в соответствии с основным профилем рельса. Пост грубой шлифовки представляет собой кабину, оборудованную местной приточно-вытяжной вентиляцией.
Комплект шлифовальных машинок для поста грубой шлифовки включает одну напольную и две подвесные.
3.9. Усилие, необходимое для дальнейшего движения уже сваренной рельсовой плети по ходу линии сварки рельсов обеспечивается установкой тянущей типа УТ-02. Приводы секций при этом автоматически отключаются, что обеспечивает экономию электрической энергии.
С помощью установки УТ-02 рельсовый стык подается на операцию термообработки сварного стыка.
3.10. Термическая обработка сварного стыка производится на комплексе высокочастотном индукционном нагревательном типа УИН.
Процесс термообработки заключается в равномерном нагреве всего сечения рельса в зоне сварного стыка до заданной температуры с последующей закалкой путем принудительного охлаждения сжатым воздухом.
Блок управления технологическим процессом термообработки обеспечивает полную автоматизацию с минимальным участием оператора и реализует следующие функции:
- управление комплексом в двух режимах - ручном и автоматическом;
- задание и контроль параметров термообработки (температуры нагрева, времени нагрева, мощности преобразователя частоты, времени закалки, давления воздуха в закалочном устройстве);
- контроль технического состояния оборудования комплекса по сигналам с датчиков и концевых выключателей;
- создание, накопление и хранение паспортных данных (информации о протекании процесса термообработки) на каждый сварной стык с возможностью их распечатки;
- создание сменного рапорта по результатам работы комплекса за смену с выдачей заключения по каждому стыку (годен / не годен) с возможностью распечатки на принтере после окончания смены.
3.11. Дополнительное охлаждение стыка производится на установках воздушного и водяного охлаждения.
3.12. После термообработки и охлаждения производится холодная правка сварного стыка на установке типа УПСХ-01 для приведения его к требованиям стандартов по прямолинейности.
На установке производится правка рельса в горизонтальной и вертикальной плоскостях на базовой длине 1300 мм, с контролем прогиба рельса лазерными датчиками на длине 750 мм. Установка позволяет пропускать изолирующий стык с комбинированными металлокомпозитными накладками.
3.13. Окончательное шлифование сварных стыков по поверхности катания и боковым граням производится на посту чистовой шлифовки типа ПЧШ-01.
С помощью шлифовальной машинки производится окончательная доводка сварного стыка до требуемой геометрии и чистоты. Пост чистовой шлифовки представляет собой кабину, оборудованную местной приточно-вытяжной вентиляцией.
После чистовой шлифовки стык охлаждается на установке водяного охлаждения.
3.14. Дальнейшее движение рельсовой плети по линии сварки обеспечивается транспортером тянущим модульным типа ТТ.
Транспортер тянущий предназначен для работы в составе технологической линии рельсосварочного предприятия для транспортировки длинномерных рельсовых плетей. Система управления транспортера выполнена на современной элементной базе. Скорость движения длинномерной рельсовой плети, тяговое усилие транспортера задаются частотно-регулируемым приводом.
В зависимости от длины рельсовой плети, транспортер тянущий может быть выполнен в двух исполнениях: ТТ-02, состоящий из четырех модулей, и ТТ-03, состоящий из 5 модулей.
3.14.1. Перед тянущим транспортером устанавливается специальная секция, на которой производится сбалчивание предыдущей и следующей рельсовой плети с применением специальных накладок для затаскивания плети на специальный рельсовозный состав.
3.15. С помощью транспортера сварной стык подается на операцию дефектоскопии.
Контроль качества сварных стыков рельсов осуществляется автоматизированным многоканальным дефектоскопом ультразвукового контроля МИГ-УКС. Дефектоскоп производит проверку всего сечения рельса (в том числе перьев подошвы) 86-ю каналами контроля. Схема ультразвуковой проверки стыка делает возможным обнаружение дефектов различной формы и ориентации. Искательная система включает в себя пять блоков резонаторов, один из которых располагается на поверхности катания головки рельса, два на боковых поверхностях головки и два на верхних поверхностях перьев подошвы. Перед контролем сварного стыка производится автоматическая проверка наличия акустического контакта под каждым датчиком. Результаты контроля каждого стыка сохраняются в памяти дефектоскопа в виде протоколов. Программа отображения дефектоскопа МИГ-УКС позволяет просматривать и распечатывать протоколы контроля, содержащие подробную дефектоскопическую и служебную информацию по всем каналам и сформировать электронный паспорт плети.
3.15.1. В случае забраковывания, сварной стык возвращается на операцию вырезки стыка. Вырезка осуществляется рельсорезным станком типа РР-302, расположенным в технологической линии между постом грубой шлифовки и постом термообработки стыка. Затем концы плети возвращаются на участок зачистки контактных поверхностей.
3.16. После прохождения ультразвукового контроля, сваренная плеть с помощью тянущего транспортера подается на транспортер-распределитель плетей типа ТРП-01.
3.17. Используя поворотные направляющие транспортера-распределителя, плети укладываются на специальный рельсовозный состав, который осуществляет транспортировку длинномерных рельсовых плетей к местам укладки.
4. Технологический процесс линии восстановления рельсов
4.1. Поступающие старые рельсы разгружаются в специальной зоне складирования, где производится их предварительная проверка и сортировка. Рельсы сортируются в соответствии со стороной головки, подлежащей фрезерованию.
4.2. Пригодные для дальнейшего использования рельсы укладываются на приводной рольганг и подаются на участок очистки, где металлическими скребками и щетками осуществляется очистка от грязи и ржавчины всей поверхности рельсов.
4.3. Очищенные рельсы подаются на операцию правки. Правка осуществляется в двух плоскостях рельсоправильным прессом типа DRH 700 с кантователем типа RR36.
4.4. Приводным рольгангом выправленные рельсы подаются на участок ультразвуковой дефектоскопии, где выявляются внутренние дефекты рельсов, такие как трещины, расслоения и т.п.
Ультразвуковая дефектоскопия рельсов производится дефектоскопом типа USF6 при перемещении рельса на небольшой скорости.
4.5. Все выявленные дефектные участки рельса, а также зоны с болтовыми отверстиями вырезаются на рельсорезном станке типа SC-800 или PP-302. После вырезки рельсы должны иметь длину не менее 7 м, в противном случае они отправляются в металлолом.
4.6. Пригодные рельсы поступают на рельсофрезерный станок типа PRV 250 для репрофилирования изношенной головки рельса, т.е. поверхности качения и боковой поверхности головки рельса. Фрезерование головки рельса осуществляется при движении рельса под фрезерными головками, что позволяет фрезеровать рельсы любой длины. Одна фрезерная головка обрабатывает поверхность качения головки рельса, другая – боковую грань головки рельса.
4.7. После фрезерования рельсы приводным рольгангом подаются на накопительно-передаточный шлеппер и перемещаются к линии сварки.
5. Охрана труда
Производственные процессы на рельсосварочном предприятии относятся к 2б и 1а, 16, 1в группам производственных процессов согласно СНиП 2.09.04-87.
Обслуживающий персонал обеспечивается санитарно-бытовыми помещениями согласно СНиП 2.09.04-87 (п. 2.5), медпунктом, помещением для приёма пищи.
Технологические потоки для производства рельсовых плетей работают в полуавтоматическом режиме, оборудованы системой блокировок, световой, звуковой сигнализациями и радиосвязью.
Освещение производственных участков, вспомогательных и административно-бытовых помещений соответствует нормативным требованиям по освещённости. На постах зачистки, сварки, грубой и чистовой шлифовки, дефектоскопии предусматривается индивидуальное освещение рабочих мест.
Выделяющиеся на постах зачистки, сварки, грубой и чистовой шлифовки пыль и вредные газы локализуются и удаляются через систему циклонов и фильтров местной вытяжной вентиляцией. Все производственные, административно-бытовые и вспомогательные помещения оборудуются общей обменной приточно-вытяжной вентиляцией.
Производственные процессы на линии не сопровождаются излучением шума выше допустимого уровня. Для погашения шума от установленных в производственных помещениях вентиляторов, на всасывающей и нагнетающей сторонах устанавливаются трубчатые глушители.
Для обеспечения электробезопасности предусмотрено устройство контура заземления и подключение к нему металлических частей оборудования и конструкций.
Тепловой режим в производственных, административно-бытовых и вспомогательных помещениях обеспечивается системой отопления, кондиционирования, общей обменной вентиляцией и соответствует установленным нормам.
Сварочные машины оборудуются защитными экранами, предотвращающими распространение искр, образующихся при сварке.
К работе на производственных участках допускаются специально обученные, аттестованные лица, не имеющие медицинских противопоказаний.
Весь персонал рельсосварочного предприятия должен проходить инструктажи по технике безопасности и соблюдать установленный технологический регламент.
Погрузо-разгрузочные работы на рельсосварочном предприятии будут производиться средствами малой механизации (платформенными тележками, гидравлическими кранами, самоходными штабелёрами и электропогрузчиками).
Рельсосварочное предприятие оборудуется внутренним противопожарным водопроводом согласно СНиП 2.04.01-85*, первичными средствами пожаротушения и охранно-пожарной сигнализацией.
Принятые технические решения обеспечивают безопасную для жизни и здоровья людей и окружающей среды эксплуатацию объекта.
6. Характеристика энергетических средств
Наименование |
Техническая характеристика |
Источник |
Регламентируемые показатели |
Единица измерения |
Электроэнергия | 380V, 220V, 50 Hz | КТП | 380V, 220V, 50 Hz | MWt, MWt/h |
Вода хозяйственная и питьевая | 0.6 Mpa | наружная сеть | - | m3 |
Сжатый воздух | 0.8 Mpa | компрессорная станция | 0.8 Mpa | m3 |
Оборотный воздух | 0.6 Mpa | Водооборотная система | 0.6 Mpa | m3 |
7. Перечень оборудования
7.1. Рельсосварочная линия
- станок для зачистки контактных поверхностей типа СЗ-03 с фильтровентиляционной установкой;
- рельсорезный станок типа РР-302;
- рельсосверлильный станок типа Robel 1035;
- рельсосварочная машина типа МСР-63.01А;
- установка правки горячих стыков типа УПС-02;
- пресс малогабаритный специальный типа ПМС-320;
- пост грубой шлифовки типа ПГШ-01;
- установка тянущая типа УТ-01;
- комплекс высокочастотный нагревательный типа УИН;
- установка воздушного охлаждения сварного стыка - 5ЯТ.431.007;
- установка водяного охлаждения сварного стыка - 5ЯТ.431.006;
- установка холодной правки стыков типа УПСХ-01;
- пост чистовой шлифовки типа ПЧШ-01;
- транспортер тянущий модульный типа ТТ-02 (ТТ-03);
- многоканальный дефектоскоп типа МИГ-УКС;
- дефектоскоп переносной типа Авикон-2Р;
- распределитель рельсовых плетей – транспортер-распределитель плетей типа ТРП-01;
- секции рольганговые приводные типа СУРТ-01;
- машина ручной шлифовки типа МРШ;
- таль электрическая модель 12ТТ11;
- тележка платформенная с механизмом подъема LEMA модель LVF;
- кран гидравлический передвижной LEMA модель LMP10;
- электропогрузчик: модель LMQOH2060TX.
7.2. Линия восстановления старогодных рельсов
- рельсоправильный пресс типа DRH700;
- кантователь рельсов типа RR36;
- ультразвуковой дефектоскоп типа USF6;
- рельсорезный станок типа SC800 (PP302);
- рельсофрезерный станок типа PRV 250.